The story
If you want to make your own battery packs from LiIon round cells, then you have to solve the problem of connecting the individual cells. Soldering leads to them is not an option, because the required prolonged heat at the battery tabs tends to damage the cell's inner structure.I faced exactly this problem, and learned that the most common method to interconnect the cells is to weld nickel or nickel-plated steel strips across them using resistance spot welders.
The working principle of these is to push electrical current through metal strip and battery tab. As the metals have an electrical resistance, this current causes the material to melt together. The molten metal should only occupy a small area to prevent damage to the battery. This is accomplished by using a high current, allowing for very short pulses.
As this is a challenging task to achieve, professional welders start at several 1000$. There are cheaper models from a Chinese company, but I decided against this option... As I am an electronics engineer with quite some experience in power electronics, I decided to develop my own welder. It should be affordable for DIYers, more powerful and robust than comparable designs, and simple to use.
And I didn't like the fact that seemingly all spot welders would use a preset pulse length to set the weld intensity. The flowing current typically cannot be regulated, instead it varies with the electrical resistance of the weld spot itself. And that depends on quite a few factors like contamination, corrosion, and the mechanical force at which the metals are pushed together. The result is a variation in the amount of energy (=heat) that goes into the weld, leading to inconsistent results. To mitigate this effect, modern welders use two or more pulses, in order to soften the metals and burn away any contamination.
But there is a much more straight forward way to obtain consistent welds: If the amount of energy that is dumped into the weld spot is kept constant, then the same amount of metal is molten each time. This is what kWeld does. There is no need to experiment with time intervals, or the number of cleaning pulses. You just dial in the desired energy amount, and start working. The unit automatically adjusts the pulse duration to achieve the same result with each and every weld.
This picture shows the result of welding 0.15mm nickel strips to 18650 cells (source: eevblog forum, user "romantao"):
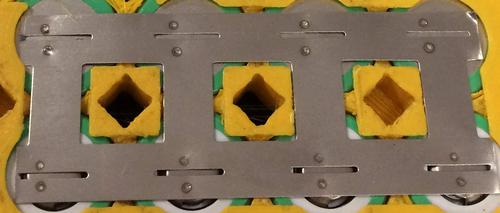
With the right power source, the kWeld unit is capable to weld pure nickel strips of up to 0.3mm thickness. But it is also agile enough to weld thin copper wires at low energies. The following picture shows a thin copper strand welded to a 2mm steel rod:
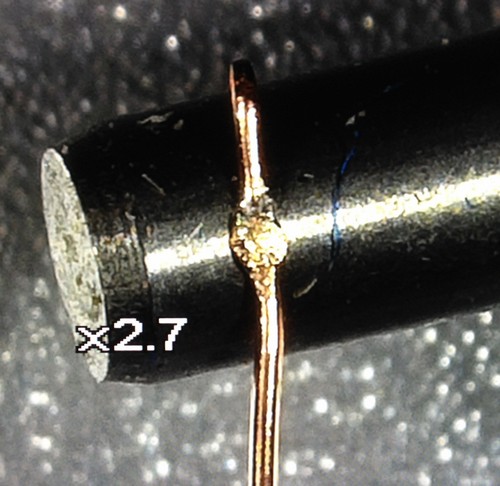
Where can I get it?
The kWeld system is available in kit form for self assembly in my shop: https://www.keenlab.de/index.php/product-category/kspot-welder-kit/The assembly and operating manuals are available for download here:
https://www.keenlab.de/wp-content/uploads/2018/07/kWeld-assembly-manual-r5.0.pdf
https://www.keenlab.de/wp-content/uploads/2018/07/kWeld-operation-manual-r3.0.pdf
The system firmware is upgradeable, allowing you to benefit from new features or improvements.
The latest firmware is available for download here:
https://www.keenlab.de/wp-content/uploads/2019/01/190128_kweld_release_r2_9.zip
This tool https://www.keenlab.de/index.php/product/kweld-firmware-update-tool/ is required to connect kWeld to a computer.
The necessary power supply for the welder is not part of the kit. It should ideally have an output voltage of 5 to 15V DC, and it should be able to deliver at least 1500A of current when short circuited for a few tens of milliseconds. As this is quite challenging to achieve, the following list gives some recommendations:
- Turnigy nano-tech 3S/5000mAh/130C Lithium Polymer battery (link). I have stress tested one of them for several complete discharge cycles, and it shows no visible swell thereafter. The measured current is 1300-1500 amperes.
- Turnigy graphene 3S/6000mAh/65C Lithium Polymer battery (link). These do not show any swell after a few full power discharge cycles, but I have no data on their life span yet. The current level is comparable with the nano-tech model.
- Ultracell UXL65-12 (link). According to feedback from a user, the current reported by kWeld is approx 1000A when tested with 0.15mm nickel strips.
- Bosch SMT 31-100 (link). According to feedback from a user, the welding current reported by kWeld is approx 1400A.
WARNING: Lithium Polymer batteries are potentially dangerous. If they fail internally, they can spontaneously self-ignite. It is therefore strongly advised to permanently supervise them during use and also while charging them, and to store them in a fire safe container when not using them.
You are dealing with very high energy levels when using this system, which may result in personal injury or fire when handled improperly. Take appropriate safety measures and use this system with caution. Never leave it unattended while being powered.
This product contains small parts, keep out of reach of children!
This system produces significant magnet fields, do not use it when you have a cardiac pacemaker!
The specs?
Hardware features (new features are highlighted in bold):- Input voltage for welding: 4V - 30V DC, enabling the use of ultracapacitors
- Extremely rugged MOSFET-based power switch and mechanical current bus design
- Fused overvoltage protection of internal power supply
- Maximum switch current: 2000A
- Power switch internal resistance: 120µOhm
- Pulse duration hardware watchdog: 250ms
- Undervoltage lockout for power switch transistors
- Input voltage, output voltage, switch current, and logic supply voltage measurement
- Logic supplied directly from main power source - no need for a separate auxiliary power supply
- Screw terminal for external trigger switch
- Logic supply holdup capacitor during pulse firing
- user interface via an LCD, a dial/encoder, and a beeper
Software features (new features are highlighted in bold):
- Central weld control algorithm uses a Joule metering approach instead of a simple timer, eliminating the need for two-pulse firing and providing more consistent welds - the amount of energy that is deposited into the weld spot is always kept constant
- Ability to detect a failed weld, and acoustic feedback to the user
- Calibration procedure to cancel out electrode lead losses
- Manual mode, triggered from external switch
- Automatic mode, accompanied with a warning sound and triggered with an adjustable delay, once the system detects that both electrodes are in steady contact with the weld material
- Audible feedback of weld process completion
- Numeric feedback from an executed weld, assisting the user to achieve best results: pulse count, deposited energy amount, required pulse time for this energy, measured current flow, measured ohmic resistance of weld spot
- Simple and intiuitive user interface - just adjust the desired weld energy up to 500 Joules with the dial knob; experience fine control from the use of an encoder
- Configuration menus accessible via dial's push button
- Overcurrent monitoring aborts pulse when triggered, protecting the power switch
- Battery monitoring with adjustable warning voltage
- Fuse fitness monitoring
- Firmware update interface
Please also check out
https://endless-sphere.com/forums/viewtopic.php?f=14&t=89039http://www.eevblog.com/forum/projects/guesses-on-what-i-am-attempting-here/
as well as these videos discussing the evolution of this system:
https://youtu.be/Ceos88VO6p4
https://youtu.be/fWXphoDE_H8
https://youtu.be/JR3GJYScquc
https://youtu.be/9-CQd02EDIs
https://youtu.be/rQnODV4VQjU
Hello,
when you can actually send complete kit, housing and firmware update tool ?
Well thank you!
When you send the kit? At week 12 (19-25 of march) or in the 12 month of 2018?
It is actually week 12 of this year, 19-25 of March.
When i got the welder after correctly assembling it I connected it mistakenly with wrong polarity.It blew some diodes even so it still worked.After contacting Frank he recomended to replace the blown diode with new ones if I was able to solder it.He offered to send me new diodes.He sent me another e mail warning me not to use the welder without the diode protection.The soldering was just to difficult for me , so I sent it back to Frank.It came back to me repaired at no extra cost apart from postage naturally!! That is what I call exellen t customer service !! all communication was always answered promptly and advice was always freely available.
The welder works extremely well
Thank you Frank
Hi Frank, I forgot the name of the ebay seller that sell the K-Weld here in the US. I bought the K-Weld from him and I want to get in touch with him so I can get the files for the enclosure so I can have it printed. I also need to get firmware cable do update. Has there been any update in the last 18 month? If you can email me the US seller info that would be great. My email is ishmerc@yahoo.com
Thank You .
Very nice product.
Regarding the actual welds (say using the common nickel strips), what is the conductivity/resistance of each weld “spot”? Has this been measured?
Thanks in advance.
Thanks! The welder measures this with each pulse (it needs to know it to be able to do the energy metering), and the displayed values are typically between 1 and 3 milliOhms.
How much is it
Received My Kit today what a nice peace of engineering was welding 1/2 hour later Welds like a gem. Great instructions clear & easy to read even for dummy like me.
Like to thank you guys will buy more as I will make A table setup for this unit as I have been repacking batteries for 35 years
Shipping To Australia was so Quick Thank you again will be buying more of this item.Frank you saved me lots of heartache great Service.
Regards
Peter Goulding
Australia
Hi Frank,
I received my kWeld unit. I have a few questions. Can you please check your email?
Thanks,
Larry
Hi Frank,
I would like to order the complete kit. when will it be available?
Best regards,
Moe
Bonjour
je viens de passé commande, pouvez-vous me donné une date de livraison?
Merci Vincent
I have iedereen the complete kit andere housing. When van i expect IT and is there a track and tracé tot follow the shipment?
Great tool, great design, great service, great manuals, workshop great.
Thanks Frank foto tour support.
Hi Frank. When do you anticipate having stock to sell? I will order a complete kit complete with housing and spare electrodes as soon as you can handle an order from Oz sir.
New material is ordered and will arrive end of Nov2018 if everything works smoothly. I’ll inform through the newsletter once I am ready to ship.
What would be a better power source? A 3s 11.1v lipo Graphene 75c or a 14.4v 4s lipo 75c…?
A 3S Lipo with at least 300A rated current should be used. This means, a 75C battery should have at least 300/75 = 4AH of capacity. The more, the better and the less risk of damaging the battery from the high current pulses.
Please also have a look at the product page where I give some recommendations: https://www.keenlab.de/index.php/portfolio-item/kweld/
4S also works and will deliver even higher current, but more voltage increases the likeliness of arcing and excessive electrode wear, and more current isn’t healthy for the battery.
Hi Frank, My order has just arrived, not long to get here in Australia. Now to put it together and have a play. Thankyou sir. Nick
Frank for some reason your link to http://www.eevblog.com/forum/projects/guesses-on-what-i-am-attempting-here no this page is no longer is working and is wanting a forward slash at the end of the URL.
However http://www.eevblog.com/forum/projects/guesses-on-what-i-am-attempting-here/ is working fine.
Thanks for pointing this out, corrected!
Hallo Frank,
Ich habe jetzt mein erstes Akkupack (zwar nur 4 Zellen) geschweißt, und das funktioniert einwandfrei, schnell und unkompliziert.
Als Stromquelle verwende ich eine Autobatterie, die ich sowieso rumstehen habe.
Das Gerät ist echt toll!
Danke!
lg
Robert
Damn I wish the postage was cheaper too Australia , airmail is only like 9.80 Euro, I want the kweld but may have too settle for malectrics instead, hope u have cheaper postage one day
I’m sorry but no plans at the moment. I was shipping via DHL before but ~5% of *all* international shipments never arrived. After losing a lot of money when resending orders, and disappointed customers (some parcels took 10 weeks to arrive), I dropped that and switched to UPS. Maybe worth to mention: I’m looking for a reseller in AU!
I was wondering if anyone knew how to connect a regular desktop computer atx powersupply to this rather than the server psu.
I’ve haven’t done this before so I’m a little worried about how to do it. Or does anyone know of a guide online?
You can use the kSupply module with any 12V supply, the server PSU is just the most convenient way. Please have a look in the kSupply’s user manual (link on product page).
Hey Frank.
Thanks for your response.
Just to clarify, I would use the following from a regular atx power supply: +12V for the positive and the -12V for the negative? Also, do I do anything with the “ground” wires from the atx power supply?
Hi John,
if you would do that, then you would instantly destroy the kSupply module. Please don’t treat this as an offense, but your response suggests me that your electrical knowledge is limited. Building and using the spot welder system, and also dealing with high power Lithium batteries requires a good understanding of these topics, or dangerous situations can arise. For example, an improperly large welded battery pack can self ignite, even when used with a BMS.
Cheers, Frank
No offense taken, but yes. I am just starting to learn about this area. I’m just trying to get this up and running, so I can start with just welding tabs on first then working my way up to making my own battery packs. Any help (i.e. how to connect an atx power supply to the ksupply module) would be apprciated. If not, then no worries, I don’t regret my purchase either way. I’m looking to experiment, learn and grow. Just reading anything I can right now on batteries.
I appreciate your approach, learning by doing is great and we should have more people out there who dare doing this adventure. But I strongly encourage you doing this step by step. Take a multimeter and see what happens when you measure between the +12V and -12V wires of your ATX supply (you’ll then see why your question alarmed me, and you’ll also learn what the black wires are for). Use transistors to switch something. Learn how to program with an Arduino. Spot welding and assembling LiIon batteries is just not the right step, the welder (shortly) uses more power that your entire household, and LiIon batteries are extremely dangerous when handled improperly. Please watch this video, the only mistake that this guy made was to charge them inappropriately: https://www.youtube.com/watch?v=WdDi1haA71Q
I took a multimeter and I’m just glad I didn’t connect those two together. I’m currently going through my old text book and brushing up on circuits. Thanks for the heads up.
I like it alot. very nice. I also recommend a holder for the electrodes like the commercial versions have. Could be 3d printed and then spring tensioned so you get even pressure.
welderreview.com
Thanks for your great feedback! You might want to check out this community contribution, it is a simple holder: https://secondlifestorage.com/t-Easy-to-3d-print-K-Weld-electrode-housing-files
Got delivery today! Thanks, been wanting this one for a few years now!
Hello!
Great kit, swift delivery to Sweden, easy to assemble and clear instructions!
Tried it first time today with a Turnigy Graphene 75C 3S 5.0Ah pack. Nice welds with 0.15 nickel @ 35J. Plan to do a stress test to see when the pack starts to heat up.
Calibration data if of any use:
R=2.02mR
Con=66
Once again, highly recommended
Regards,
Alexander
@alexanderhebo – how many welds do you get per charge on your battery pack?
Hi Frank
Assembly of the Kweld laser cut transparent acrylic glass housing kit requires use of pattex or acrifix transparent glue and unfortunately it’s not available in my locality…as substitute possible to use this “weld- on” “Scigrip#16 10315 low viscosity acrylic cement”…?TIA
Checked the product description, looks good!
Expecting my kweld kit today! Is it possible to solder the cable lugs instead of crimping them? I don’t have such a large crimper, and am reluctant to buy it just for this one job. But have LOTS of soldering equipment.
Yes you can do that, use lots of solder 🙂 The connection will have a slightly higher electrical resistance.
Soldered all the lugs. The weapon of choice was a 325W Weller dual-post soldering gun. Rosin-core solder, and also a flux pen. It worked out fine. The silicone insulation laughed at the heat. About a centimeter of wire stiffened up due to solder wicking into it.
Now I need to power it. First try – a Concord aircraft battery. More or less group 24 in size, plenty of power for starter motors – or welding! Unfortunately, it is not quite as liquid-tight as it used to be, and when you pull large gobs of power out of it, it SPITS. Just a little. Just enough to burn my finger :(. A marine battery box is on order.
I do have an 83 farad super cap array – but it’s apparently only rated for 20A continuous ( which is OK ) but also only 120A peak.
Any (fresh / warm) 12V car starter battery with 65AH to 100AH should do the job 🙂
200€ for a kit including tax and part of transport is expensive will be bether to have included tax in a 167€ price
167€ + transport will be nice
over 200€ is over my walet ?
I’m sorry for that but these are my prices – with your calculation, I would not even make *any* profit anymore. Most of my stuff (all electronics) is made in Germany and I am only using branded quality components, which results in different prices when comparing to what we all got used to from China. Using local suppliers is also important for me ethically, because I think that we are all bleeding ourselves out by shifting all labor to Far East, in order to have more cash in our pockets. In my opinion this is very short sighted.
Frank thanks for the explanation if i buy your product you don’t give varanty but if my spot welder get brouken or damaget you are give suport to repair this at home? shematic or way to program brouken controler?
I’m trying to use a lead acid car battery (AGM H8).
My question is – what gauge battery lead wires should I use? I tried it with both new and 5-year old (just swapped for the new) H8 batteries for my Touareg. New I think the 1000 cranking amps translates to about 130Ah. I used what I had sitting in the garage, all-copper 16 inch 2ga starter lead wires produce overcurrent on cal. Lead length was adjusted to actual length, but I have to think it is assuming 8 gauge wire that length, so I should probably set it crazy short for the battery leads?
Or should I:
1. Use longer thin 8 AWG copper lead wires?
2. Look for a smaller battery? Question being just how small…
3. Give up, buy a lipo battery and charger just for this (and a storage bag for the battery when not in use).
I prefer the lead-acid as I have a great charger for those already and they are very safe, but if it’s really difficult to get those dialed in to work, I’ll bite the bullet and get a lipo.
Got it sorted with the 2 AWG leads. Just needed to lower the total cable length (taking into account the size difference) to 1m total.
@janik00005: of course I do warrant for any production defect of my products, but also when you get an issue that you have caused (e.g. accidental short circuit) I’ll do my best to help you out wherever possible. In the latter case I’d ask you to carry the shipping cost of course. If you have the tools to repair it yourself then I’ll provide guidance, but schematic/firmware are closed source.
Good support is great 🙂
If i power up my kWeld from to weack power supply i will damage my power supply and kWeld or only power supply?
can I ask you to contact me via email for these more detailed questions, frank.boeh@keenlab.de ? That would allow me respond much easier. To your question, this depends on your power supply- what type and model?
Fast delivery. Kit is very wellt built, proverbial German quality. I use a Lipo 7s, 5 Ah, 80C which delivers approx. 1600A. With this setup I can weld together 4 pieces of 0.15mm pure nickel strips at only 15 Joules.
Frank,
Have you any recommendations for using the “copper sandwich” welding method with kWeld? That is to lay a .15mm nickel tab on top of a .2mm copper tab and weld. I am using a 6000mah Graphene Turnigy (Panther) battery which seems to deliver ~1400A. Around 75ms I am able to get it to stick reliably to a steel blade (recommended for testing settings), but wanted to get your feedback on this use.
I’ve done tests in the past, but the amount of current that kWeld can handle doesn’t seem to be enough for working with copper due to its much lower electrical and thermal resistance. This asks for pulse laser welder, for example. Some users experiment with nickel-copper-nickel sandwiches (*not* plated copper), which works apparently.
Hi Frank, I am thinking about putting 30 of your super-caps in series for a max. of 72v. I’ve found some balancing boards that could fit.
The reason I want this is to have more inrush current available for my cable cart motors and also to act as a filter because the HiFi in my house is connected to the same 20s LiFePo4 battery-pack.
But here my question: what about welding them together with the “K-Weld”? How much joules it would need?
I have some heavy LiPo packs, I can put in series/parallel.
I have 4 pieces: 12000mAh 20c 6S 22.2V
And I have 2 pieces: 16000mAh but I must check at home about the current they can handle.
I could also use my LiFePo4 batteries. I have 20 in series of 200Ah; they can handle max. 400 amp.
Any tips, idea’s?
kWeld is a spot welder, but welding the BCAP0650’s requires a continuous material stream like that of a TIG welder.
Suddenly I think it is easy to do without welding, just putting all in series fixing with tie wraps and only putting a busbar at the beginning and the end.
But than what about the balancing: I saw a screw on the side, probably to connect to a balancing circuit; can somebody confirm me this is the case? Because I can’t find any datasheet that shows or talks about this screw.
Hi Rudy,
would you mind to contact me via email (frank.boeh@keenlab.de), which would be less effort for me to reply to you?
When you consider a mounting method, please keep in mind that the cells cannot handle axial force on their terminals, as this puts the seals under tension. And I think that this screw is used during production to fill in the electrolyte.
Cheers, Frank
I mean putting in series against a angled bar to keep them in place is easy. Than on both ends putting a busbar that is put under tension with a bolt. The only problem is insulating. Maybe gluing a PVC angled bar inside. Also to put tension between the first and last capacitor I need to find a way to connect and insulate. Maybe a wooden box? Or making something out of fiberglass that is fits the + and – electrodes on both ends and can be attached to the angled bar.
Do you no longer ship to the UK? There is no UK option at checkout ?
Hi Dave,
I’m really sorry but I had to stop shipping to UK after Mr Johnson’s plans after Brexit. Long story, but you’ll notice that many other international sellers have stopped this as well. I’m looking for a UK reseller, but that needs time.
The UK government wants me to collect tax from UK consumers, report and remit this quarterly, and even to have my business registered in the UK. That’s unique among *all* countries worldwide. Therefore: can’t do anything at the moment. The list of business contacts that told me that they have stopped selling to the UK is getting longer and longer…
Cheers, Frank
Hi Frank,
I wanted to order a kweld and kCap for my UK company. I have a VAT/EORI number. I think if you have that, there is no problem. Maybe stipulate that as an order requirement.
I’d also be happy to talk about being a reseller, if it’s mutually beneficial.
Stuart.
That’s correct but I’d have to manually sort out such orders as selling to consumers in UK is no longer possible for me after new UK rules for foreign sellers. I’m setting up a UK reseller that I’d like to you contact: kocurmarcin@wp.pl
The EU are doing the same thing from 1st July. Anyone selling to the EU must collect VAT. Basic same rules. The UK just implemented it 6 months earlier, presumably because it made more sense to do it during the Brexit transition.
I noticed that the weld current is a way more important parameter than the energy. I do not get the energy story anyway. P=I^2*R when you integrate it over time you get the energy. Assuming for a low impedance voltage source the current is constant , the energy is no more than the weld time. I am trying to spotweld 0.2mm nickel tabs. I started with Lipo packs as a voltage source. That gives me the voltage and the internal resistance as parameters. Voltage is already a crude parameter using a lipo because it a multiples of say 4V, internal resistance is really a wild guess. The bad thing is also that the power increases quadratic with the voltage. Started with a 2S pack: https://hobbyking.com/en_us/turnigy-alpha-6500mah-2s2p-140c-premium-hardcase-lipo-battery-pack-roar-approved.html?queryID=aad608d5bcc29a4bf0dc869778304ff1&objectID=85619&indexName=hbk_live_magento_en_us_products, weld current was between 1.0 and 1.1kA. But clearly not sufficient to weld 0.2mm to lithium werks ANR26650M1-B. Ok so I stepped up to a 3S pack: https://hobbyking.com/en_us/turnigy-rapid-5500mah-3s2p-140c-hardcase-lipo-battery-pack-w-xt60-connector-roar-approved.html?queryID=e0df7c14aa1cf962e2b939ea725b97c5&objectID=85637&indexName=hbk_live_magento_en_us_products. Welding current is now between 1.3 and 1.4kA results are better but still it seems more current is required. So I now have ordered 4S: https://hobbyking.com/en_us/turnigy-rapid-5500mah-4s2p-140c-hardcase-lipo-battery-pack-w-xt60-connector-roar-approved.html?queryID=966cb393bfebd5f79ec0e2b38147345c&objectID=85640&indexName=hbk_live_magento_en_us_products. So assuming same internal resistance the current should be now 4/3 of what I got with 3S. All very cumbersome. So my questions is are there people that have experience with welding 0.2mm nickel strip and what current is used for the weld? I also noticed that the weld spots are not symmetric which makes sense doing a DC weld because the current distribution is not symmetric are there people with the same experience?
Hi Stefan,
“I do not get the energy story anyway” >> your assumption “the energy is no more than the weld time” is incorrect. What varies is the weld spot resistance, basically due to varying mechanical pressure and dirt or corrosion between electrode and materials. A varying resistance leads to varying injected power, which is why kWeld does energy metering to automatically adjust to these varying conditions. Classical “constant pulse” welders cannot achieve the same level of repeatability.
“Welding current is now between 1.3 and 1.4kA” >> that is more enough to reliably weld up to 0.3mm nickel. If you don’t get good results, then please try to recalibrate the unit while ensuring good contact of *the tips* of the electrodes in the second step. If you get any sparks then repeat. Make sure all nuts and bolts are tight. Don’t extend the battery leads as this results in excessive inductance. What type of cells do you weld to? Some have aluminium cans, which isn’t possible with this kind of welders – that asks for pulse laser welders or similar.
Cheers, Frank
Hi Frank, thanks for the reply. Imho variations of resistance can be due to pressure changes that is why you see often a spring mechanism. For oxides and pollution often a pre-pulse is used which could be implemented by Kweld also and would be a very nice feature. My experience with kweld is that increasing the energy with a factor of say 1.2 results in a weld time increase of a factor of 1.2 so it seems that resistance is fairly constant if other factors are constant. But anyway the cell I am trying to weld is the Lithium Werks ANR26650M1-B. The problem is welding the positive terminal. I am a little bit closer to the root cause. I took a cell apart and see that it is a aluminum can (as you are saying) with a nickel cap on the negative terminal that goes into the cell and welds very nice. The positive terminal is the complete aluminum can to which a thin nickel plate is bonded (looks soldered) that forms the positive terminal. My hypothesis is that the heat conductivity of aluminum (240 W·m−1·K−1 vs 90 for nickel) is the problem. Much of the heat is absorbed via the aluminum because the nickel plate is very thin that is why increasing the power gives better results. I hope that a weld current of 2kA will do the job. Are there possibilities to do e.g. 2.5kA if I reduce the loop area because that drastically reduces induction. Or is it possible to mount a better flyback diode to reduce the avalanche energy in the MOSFETs? Is the source code available ( I am quite familiar with STM32) ?
“variations of resistance can be due to pressure changes that is why you see often a spring mechanism”
>> That’s true, but kWeld is a hand held spot welder for customers who don’t want to spend e.g. 4000$ for a professional Sunstone welding machine.
“a pre-pulse is used which could be implemented by Kweld also and would be a very nice feature”
>> as I described, kWeld does not need that, it produces optimal repeatability because of its energy metering approach. I had tested multiple pulses, there was no benefit.
“I took a cell apart and see that it is a aluminum can”
>> I’m afraid but kWeld can’t handle that. I’d say none of the other MOSFET based DIY spot welders can – kWeld has the highest current rating among all of them.
“Are there possibilities to do e.g. 2.5kA ”
>> that’s possible, please contact me via email and I can create a custom firmware for you.
“is it possible to mount a better flyback diode”
>> you’d need multiple of them, distributed across the bus bars. Use some with at least 5kW pulse ratings. But at some point, the MOSFETs will start giving up due to unequal current sharing and electro migration.
“Is the source code available”
>> I’m afraid not.
Is there a reason why my question is censored?
sorry not correct
Hi Frank
Another though making the Kweld a real capacitive discharge welder: What would happen if I would connect 3 of these capacitors: https://eu.mouser.com/ProductDetail/KEMET/ALS70A135QT025?qs=AQlKX63v8Runp47hJ6lW9Q%3D%3D charged to 25V to kweld and set the energy to 67 Joules?
They have a series resistance of 5m Ohms, so 3 in parallel =1.7 mOhms the kweld adds another 3.3 mOhms a typical weld adds 1m Ohms so a total of 6 mOhms. A discharge of 20ms leads to a remaining voltage over the resistors of 10.6V and a current of 1700A (so within kweld boundaries). The capacitor discharged energy is 0.5*3.9(14.4)^2=404 Joules of which goes 1/6 into the weld = 67 Joules. The start current would be 25/.006 = 4166A (well within the pulsed drain current of the MOSFETs) the end current would be around 1700A within the safe inductive energy dissipation range and already considerably reduced during capacitor discharge. But with a tremendous advantage that I can influence the initial current greatly by setting the charge voltage of the capacitors. I simulated the circuit with LT-spice and a 1uH inductance and get a little bit of different values but the idea remains the same.
Kind regards,
Stefan
these cost approximately as much as 2x kCap, therefore I don’t see a benefit. But ESR and capacitance are within range, so that should be a viable option. You can’t use them at 4166A however (2000A max for kWeld), and here’s where the problems start: you would need to lower the voltage in order to stay below 2000A, and then they might not anymore store enough enery for more intense welding pulses. But why do you want to influence the current? The more the better, and constant current is optimal for repeatable results. kWeld does the rest then with its energy metering. Just make sure to stay below 2000A all the time, that’s its limit.
“You can’t use them at 4166A however (2000A max for kWeld)” >> the current when the MOSFETS are switched off is 1700A (well under 2000A) From your documentation I understand that the current limitations is because of UIS rating of the MOSFETs.
“But why do you want to influence the current?” >> Because putting more power in the weld enables to weld in situations where heat is conducted away fast, like with the famous ANR26650M1 cells. They are designed for resistive spot welding but you need higher currents than normal and I am nearly there. 1700A is starting to give reasonable results but the nudget area is still small.
What I also do not understand is why kweld cannot benefit from the fact that when a capacitor is discharged also avalanche energy is reduced. You are stressing the 2000A boundary but that is when the current is switched off or am I missing something here?
The 2000A limit is due to the need to dump all magnetically stored energy when interrupting the current. This is indirectly related to the MOSFETs UIS limit, but the system has additional TVS diodes in place and the current sharing situation is complex. The specifiction is based on actual experimentation and long term endurance tests. This limit cannot be raised without modifying the design.
” Because putting more power in the weld enables to weld” >> that’s exactly what I am saying – the more current the better. This isn’t the same as controlling/influencing the current like you asked.
“What I also do not understand is why kweld cannot benefit from the fact that when a capacitor is discharged also avalanche energy is reduced. You are stressing the 2000A boundary but that is when the current is switched off or am I missing something here?” >> Classical capacitor discharge welders suffer from the fact that the flowing current quickly drops while the capacitor is being discharged. As welding power is proportional to current squared, that drops even quicker. That’s why our kCap works differently: due to its high capacitance it is only marginally discharged, and supplies near to constant current during the entire pulse. This keeps pulse power constant, resulting in more repeatable results.
Hello i need to weld lithium pouch with copper anode and nickel cathode on aluminium bus bar.
Are the kweld is ready to that ?
Thanks
Coppe isn’t possible with kWeld, I have tested that with the full 2000 amperes that it can do. This task asks for a pulsed laser welder. LiIon cells with aluminium cans are the same story, that doesn’t work. The reason for both cases is the significantly higher thermal and electrical conducvitiy of these materials in comparison with steel and nickel.
“Classical capacitor discharge welders suffer from the fact that the flowing current quickly drops while the capacitor is being discharged. As welding power is proportional to current squared, that drops even quicker. That’s why our kCap works differently: due to its high capacitance it is only marginally discharged, and supplies near to constant current during the entire pulse. This keeps pulse power constant, resulting in more repeatable results.” >> I understand you are propagating constant current during the weld and why. Also understand that kCap has such a large capacity that it can achieve constant current and voltage during the weld. But in my case I need more power so the idea is make a pulse that ends at a current level that is safe wrt inductive energy but that starts much higher just as with CD welders. Spice simulations show that such a pulse can be 20-30ms and at the end 1800A is flowing (safe according to what you state). This means that during the whole pulse length the power is higher than what you can achieve with a constant voltage and average power can be nearly 40% increased (at the first few ms even 200%-300%) and that power is better controllable because you can control the charge voltage. If the weld quality is not sufficiently stable a dual pulse could be used. If you compare the specs with this concept you can surpass a Sunstone CD600DP with kweld.
I think I misunderstood you but now got the point. I like that idea, and this would be possible with kWeld in general. However, the unit would need to know the capacitance, and would also need to control the charge voltage. This is necessary to ensure that the current is low enough when opening the switch. But double-pulse operation wouldn’t be possible (unless using a second capacitor bank for that), and what to do when the unit needs to interrupt the current due to a fault? (e.g. the firmware aborts when detecting arcing). The MOSFETs cann’t handle much more current either, tested max is 2800A but they only survive a few thousand shots at this level.
“But double-pulse operation wouldn’t be possible (unless using a second capacitor bank for that)” >> well I see a number of options here one of them is if the pulse is very short the conductor is not completely charged. Say I have and inductance of 1uH and a resistance of 6mOhms than L/R=160u so taking a preweld puls 100uS than the current only rises to 47% of the max. Say that is 4000A you will still have not problem. But I admit your mosfets and driver must be able to do this. Other possibility is indeed to have two switches and banks looking at the Sunstone documentation I looks like they do it that way.
“The MOSFETs can’t handle much more current either, tested max is 2800A but they only survive a few thousand shots at this level.” >> depends on pulse length AUIRFS8409 datasheet states: Pulsed Drain Current per mosfet 1200A (pulse limited by junction temperature).
Yes, that isn’t a bad idea. The MCU and its internal ADC are fast enough to track the current at this speed. But still I don’t see a need to go to dual pulse. The kWeld’s working principle just doesn’t need that. I have done extensive testing of that in the past, and there was no practical benefit. The unit handles varying conditions very well as it is right now. Regarding current handling: I use to take such datasheets numbers with caution. My practical test results were different, which is why have set that limit.
Thanks Frank I was having the same idea continuously metering the current looks like a good idea. “The MCU and its internal ADC are fast enough to track the current at this speed.” >> If I look at the design I see no shunt so I expect you are now using de Rdson as a shunt. Are you willing to share what resistance value you are using for the calculation?
Yes, current is measured via Rdson. The used value varies, because we have a number of MOSFET options that we use depending on availability. Overall this is in the low three digit microOhm region.
My board have UIRFS8409. Typical 550uOhms , max 750uOhms @Vgs =10V (which is being used). So for 6 that would be between 91 and 125uOhms but would be nice to know what number you use in the software. Do you amplify this voltage? 0.1V per 1000A seems low use of the dynamic range of the AD converter.
I’m sorry but may I know the background for these questions? I would like to avoid supporting development of a competitor device, just in case.
Well I am trying to increase the weld current using capacitive discharge in a safe way for the kweld, meaning within SOA of the MOSFETs and within the tested max of inductive energy. I have a basic set-up working that does not do metering, but it would be nice to have simple and direct way of measuring the current. Now I determine the current by parameter estimation of a LT-spice model which also predicts the current but direct measurement is simpler. I am not developing a competitor device I just want to increase the applicability of Kweld. If you are interested I can send you the status via a PM.
You can’t assume even energy injection sharing between the MOSFETs. At these amplitudes, even the brass bus bars is a signifcant resistance and inductance. 2000A is the max of this arrangement, unless you further reduce inductance by shortening leads. You can’t ballpark via LTspice either, as this is a network with quite a few unkowns. Just send me an email, and I can answer your questions (also much quicker).
“Just send me an email, and I can answer your questions (also much quicker).” >> Thanks alot for that, I will.
“You can’t ballpark via LTspice either, as this is a network with quite a few unkowns” >> If I have a known measured capacity, a know voltage before discharge, a known voltage after discharge and an exact discharge time why can’t I estimate the current and overall resistance? Maybe you can explain to me where this estimate would fail and where the electrons would go?
Apart from these crude parameters I was also able to estimate internal resistance of my capacitor bank, the resistance of the electrode cables (confirmed with a kelvin measurement with my DMM6500), average fuse resistance, the electrode loop inductance, the input inductance, etc etc, If I put in a model of the SLD8S28A from Little Fuse I can even forecast the TVS peak voltage within 0.5V and the TVS pulse time within 0.5us compared to what I see on my scope. So when I change capacitor voltage and pulse time I can do an amazing good forecast of my scope image, way better than just a ball park. And agreed it may be a lumped model but it is certainly adequate to forecast pulse power on e.g. the protection diodes.
It is possible to power kWeld with two serial Maxwell 3000F 2.7V ?
Two aren’t producing enough voltage, use 3 in series. Keep all leads as short as possible (check the kWeld operating manual for that), and start with low voltage while attempting to calibrate. Watch the current that kWeld reports, avoid hitting the 2000A mark while increasing voltage.
My two cents: In principle yes, only note that the voltage of 5.4V will be too low to have sufficient weld current. BCAP3000 is obsolete as far as I know. Also note that the absolute max current is 1900A. You could use e.g. 4-5 in serial. Say you use 5, capacity will be reduced to 600F and internal resistance will be increased to 1.45mOhm. Although Aluminum capacitors are mostly resilient to inductive spiking I am not sure about these caps. Imho I do not see the benefit of the solution compared to a Lipo or kCap unless you can get them at a bargain.
@stefan-3702 (max reply level reached here): I had misread, thought that you were setting up a spice model for the kWeld power switch (as we last talked about that). Your approach should of course work well, if you can obtain accurate inductance values.
Hello Frank,
I am contemplating buying a new supply for my kWeld. The 2S 20Ah Lithium-ion Pouch cell has degraded a bit and the welds are just too weak. What are your thoughts about prismatic Lithium-ion Titanate cells? https://shop.gwl.eu/LTO-technology/Cylindrical-Lithium-Titanate-Oxid-Battery-Cell-LTO-2-3V-30AH.html#tab3
With a 1.0mR resistance it would be slightly better then your ultracapacitor module (1.1mR for a 2P) while having all the advantages of a normal battery bank.
Could you tell me why you choose a 3S configuration for the ultracapacitors?
I am contemplating a 5S configuration for the LTO cells. This would give me a nominal 11.5V, maximum 14.5V battery.
2S isn’t enough voltage for the welder. It works best from a power supply in the 12V region. Keep in mind that not only the battery ESR has to be overcome, the welder contributes ~ 3milliOhms and a typical weld spot has another 1milliOhm. Min recommended welding current is 1200A, max is 2000A (only possible when not extending the battery leads), and the battery ESR and voltage are your factors to work with. kCap is 3S2P, which generates approximately 1300 amps. That wouldn’t be the case when using less cells.
I did find your ESK8 post where you explained the 6.3V overhead and the 1.5V/milliOhm for the batteries. (https://forum.esk8.news/t/kweld-spot-welder/6926/99)
The 3S vs 4S for the kCap was primarily an economic choice I assume then? You could reach 1500A with a 4S but you decided that 1300A was sufficiënt while not increasing the product price substantially.
A 5S LTO battery would have a series resistance of 5milliOhms or lower with a maximum voltage of 14.5V. This would give me a current range of 1580A when full and 1200A when at 40% SoC. This 60% DoD would give me 0.60 * 30Ah * 11.5V = 745 200 joules -> more then enough welds for every conceivable battery.
Is there anything wrong in my assumptions?
Thanks for the excellent product!
Yes, a 4S2P kCap would have cost an extra 40€ (a bit less but close to) in purchasing an extra 4 capacitors only, not including any revenue from my side. I didn’t consider this as the better approach as I was worried that this is a too high price for this solution (you still need a charger on top of that). The solution for going-to-the-limits welding with kCap is to use two of them in parallel. That system can even hit the 2000A current limit during calibration and may require sigthly reducing their voltage for that step.
Your calculations look reasonable, with one small exception. The 745200J does not account for the system efficiency yet. Typically this is around 15%, so that number results in 111780J of welding pulse energy, or 2235 pulses of 50J each.
addition to above: 20€, not 40€.
Thank you for the feedback!
I will be ordering some new cables and electrodes very soon. I shall post my measurements of the LTO battery system on reddit’s /r/batteries and in this thread.
LTO batteries are the future of energy storage and will become a lot cheaper (and better!) in the next couple of years: https://www.global.toshiba/ww/products-solutions/battery/scib.html
How many welds can I expect @ 100J and the “Turnigy Graphene Panther 6000mAh 3S 75C” pack linked above?
Hi Frank,
I’m very interesting by this project. I’ve heard a lot about it (all good things!). Neverthess I have some questions please regarding the power supply:
– is it possible to use a standard 12V car battery instead of the 3S Lipo? which min-max amps?
– or, to use a portable car starter/booster? also which min specs?
I have the impression it should be possible but I didn’t read anything on that, so I prefer to ask.
Thx.
Hi I cannot send you email..have questions..was this on my end?
Greetings, is the webstore still active in selling the product?..It seems that I cannot send my email inquiries..
Hi there, you got email..
I’m not sure where you’re getting your info, but good topic. I needs to spend some time learning more or understanding more.
Thanks for excellent information I was looking for this info for my mission.
I’m not sure where you’re getting your info, but great topic. I needs to spend some time learning much more or understanding more.
Thanks for wonderful information I was looking for this information for my mission.
hello.
what is he recommened lenght for the probes? I ordered the loose kit (cables are not crimped, no problem for me), but what is the lenght of the cables – page 4 of the manual as I have 1 meter of cable.
silly question, but I think the cable lenght is important.
thank you for your time!
you can split this into pieces as you like, the welder will measure the output leads during calibration. The ‘stock’ lengths are 41cm + 39cm + 11cm + 9cm.
Hi, just purchased your kit. After finally getting a battery combination that calibrated without an over current warning (BMW lithium car battery) I blew my fuse.
Two questions.
1) Can I use an external fuse holder in my positive supply line and put a shunt where the fuse normally goes? This would make fuse replacement much easier in the future.
2) Can I use any ANL 300A fuse? Or is your circuit expecting a certain type (maybe one of a known resistance).
Thanks
you can do that, and use any 300A fuse. Mount the power cable to the right terminal, and run a thin wire to the left (logic supply only).
Frank hi – is it possible to answer me after 10 messages ? thanks
See all my emails from Radoslav Dayarski
Thanks
she answered to your messages? i want to put an order but i don’t know if she will send… nobody answer to my mails…
Hi guys, that was sorted in the end, and I’m pushing my support guy Rado to fulfill my request to answer within 48 hours. I am also more closely monitoring his activity, and make sure that this does not happen again. Regards Frank
Frank you can watch my channel here as example: https://www.youtube.com/watch?v=K1HZs4ix_6s
Hey guys!
I love the welders I bought but I have a stupid question, what is the best way to grind the tips after a while? Is it just to use a small bench sander or is there another machine or equipment that you can recommend?
Best Regards!
I use a hobby rotary tool with cutting disc (sand based) in combination with a power drill. I insert the electrode in the drill, and let both tools run. I let the tip touch the spinning cutting disc on it’s side surface. This way you can easily reshape the tip while maintaining perfect roundness.
Hi I am interested with the products..please send me mail so I can place a order..I am from UAE
val.bilegjr@gmail.com
We ship worldwide to most locations, feel invited to just go to our webshop for ordering. Regards Frank
Really good spotwelder, i must admit i’ve never used a really high power one before but unlike the one i had this one always puts down consistent welds and can do much more power even as voltage gets lower on a hobby lipo
Hi Frank, I forgot the name of the ebay seller that sell the K-Weld here in the US. I bought the K-Weld from him and I want to get in touch with him so I can get the files for the enclosure so I can have it printed. I also need to get firmware cable do update. Has there been any update in the last 18 month? If you can email me the US seller info that would be great. My email is ishmerc@yahoo.com
Thank You .
I am not aware of an ebay seller, we don’t use that platform. The US reseller is https://gridrewired.com/collections/all , this info is placed prominently on all product pages. The firmware has been stable over the last time, but I am working on a new Pro model with new features that I also want to back port to the DIY model 🙂 The new feature will be a weld quality control, based on the measured waveforms.
Ik heb enkele jaren geleden en komplete set gekocht en heb het juist aangesloten en vindt dat het prima werkt.
This een van de producten dat heel goed functioneert. Goed gedaan Frank.
Groetjes uit België
Excellent packaging!
Excellent and immediate communication.
The product is definitely perfect!
Congratulations!
I ordered the Turnigy nano-tech 3S/5000mAh/130C , and from what I see, it comes with an XT90 connector. Is that enough for the short Ampere spikes, or should I replace it with an XT150 connection?
XT90 is good enough for casual use, but you cannot bring the system to its limit with it. Please check the connector’s temperature (as well as that of the battery) periodically to prevent overheating, and reduce working speed as needed.
Thanks Frank. I only have to make some simple battery packs with 0.15mm nickel, and zbattery.solutions recommends a 36J setting for that, so I guess I’ll be pretty far from the limits. Will keep an eye on the temperatures. Calibration doesn’t take it to its limit yet I assume?
That’s all correct!
Thanks a lot. Great service!
It is more than word!
I am not sure where you’re getting your information, but great topic. I needs to spend some time learning much more or understanding more.
Thanks for great info I was looking for this info for my mission.
Hello,
I’m in the U.S.A.
Is it possible to order direct from you?
Thank you.
The CA/US reseller has an exclusivity deal, I’m afraid but you can only order from them.
https://gruzchikivesy.ru/
I recently tried [url=https://www.cornbreadhemp.com/products/full-spectrum-cbd-gummies ]full spectrum cbd gummies[/url] after the blue ribbon prematurely and was pleasantly surprised past the results. Initially skeptical, I initiate that it significantly helped with my desire and be in the land of nod issues without any notable side effects. The grease was unoppressive to speak, with definite dosage instructions. It had a merciful, vulgar grain that was not unpleasant. Within a week, I noticed a marked increase in my blanket well-being, ardour more relaxed and rested. I comprehend the regular technique to wellness CBD offers and plan to pursue using it.
I ordered my kweld a few weeks ago paired with one of the recommended batteries from the recommended site. during the calibration the battery sparked smoked lit on fire and went to 0v.
I sourced another battery locally and plugged it in. the welder did work this time and I treated it with maximum care. after a few welds the welder went into timeout, stopped welding and only showed 350A. from then on it’s just been behaving oddly. sometimes it says overcurrent and sometimes it says undercurrent but whatever it says it doesn’t let me calibrate it anymore.
i checked some resistances and one component (that i don’t know the name of maybe it’s a mosfet) has 50% more resistance than the other ones.
i’ve checked time and time again and i’m sure i’ve done nothing wrong in the building and usage of the welder.
I contacted your support through email and they said that I should replace the component on my own (mosfet diode). When I asked how to change it they just didn’t reply anymore. I found the part, bought it, and soldered it just to find out nothing changed resistance wise and the welder keeps being underpowered even though it does let me calibrate now.
I have tried using other recommended batteries too but it just doesn’t want to weld. Keep in mind my cable length is 1.4m so it’s not normal that a recommended battery that should output 1500A only outputs 350A and a super overpowered one i tried only gets to 800A. I have dumped a ton of time and money into this and honestly i’m really disappointed with the welder itself, with the customer support that left me on my own and with the recommended battery blowing up potentially making me risk my house…
update: I have received a reply from customer support!
Is it possible to use this welder with a non-battery power source? I was thinking something like the output from an actual welder?
I’m aware of the kCap module, but would a large transformer (say from a welder) not be able to supply the kWeld unit directly?
Nachdem ich verschiedene Punktschweißgeräte ausprobiert habe, von günstigen DIY-Optionen bis hin zu fast gleich teuren Geräten mit Kondensatoren, habe ich mit dem kWeld endlich ein zuverlässiges Gerät gefunden. 0,3 mm dicke Nickelstreifen? Mit kWeld kein Problem!
Das Modell mit Kondensatoren, das ich von Amazon ausprobierte, ging nach 5-6 Schweißpunkten bei 0,25 mm Nickel immer die Puste aus. Ich musste 10 Minuten warten, bis es wieder aufgeladen war. Zudem waren die Schweißpunkte keinesfalls zuverlässig und wirklich fest. Die billigen 30€ China-Geräte liefern nicht genug Leistung und brennen gerne mal unerwartet durch.
Dank mehrerer informativer YouTube-Videos über das kWeld Punktschweißgerät entschied ich mich für den Kauf und habe es nicht bereut. Es liefert außergewöhnlich zuverlässige und perfekte Schweißpunkte und bewältigt sogar 0,3 mm dicke Bleche ohne Probleme. Für jeden, der DIY-Akkus aus 18650 oder 21700 Zellen herstellt, sind mit diesem Gerät 50 oder mehr aufeinanderfolgende, wirklich gleichbleibende perfekte Schweißpunkte mühelos zu erreichen.
Absolute Kaufempfehlung!
Hi Frank.
As the fuse is an ANL 300A one and the system is able to deliver 2000A, wouldn’t it make sense to add a latency delay after each pulse?
For ordinary low energy pulses, it would be unnoticeable and, for high pace high energy pulses, it would protect the fuse.
If one wants to keep the 50% buffer of the fuse as safety margin, the latency delay could be computed as:
Delta_t = ( (I / 300A) – 1) * Pulse_t
where I is the average pulse current, Pulse_t is the duration of the pulse, and Delta_t is the latency duration during which another welding pulse should be prevented.
Luc
thanks Luc, this is a very good improvement idea. However, as we’re working on capacitor based a next generation products (both DIY and professional), I’m not sure if I can find time to execute it.
Did someone used a big (microwave) transformer and high current bridge rectifier – this possibility is mentioned in the manual page 6:
“This setup delivers a discontinuous voltage and current. As the kWeld system measures
output power with a very high update rate of 100kHz, it should still be possible to
produce consistent welds. However, this is yet to be confirmed.”
I would want to know at least what are the chances, before splurging quite some cash on a bridge rectifier in that current range.
That hasnt been done practically as far as I know. I was always discouraging from this because a rectifier that can handle such an amount of current is quite big and expensive, making this solution not very attractive.